Fracture Toughness Improvements
The fracture toughness of the halloysite particle modified epoxies was noticeably increased, with the greatest improvement in KIC up to 50% and in GIC up to 127%. The improvements in fracture toughness are mainly attributable to mechanisms such as crack bridging, deflection and plastic deformation of the epoxy around the particle clusters.The fracture toughness of the halloysite particle modified epoxies was noticeably increased, with the greatest improvement in KIC up to 50% and in GIC up to 127%.
The improvements in fracture toughness are mainly attributable to mechanisms such as crack bridging, deflection and plastic deformation of the epoxy around the particle clusters.
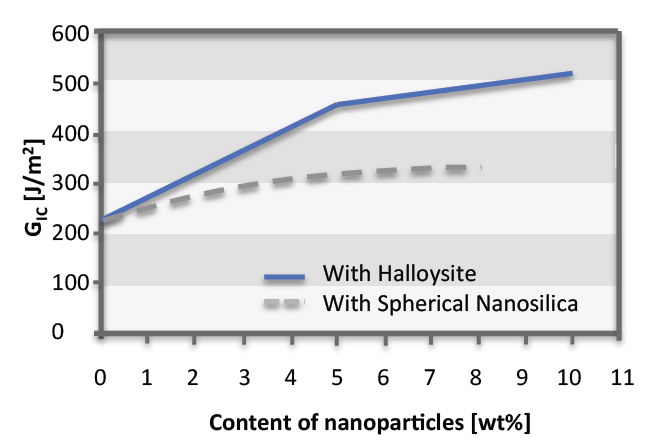
Deng, S., Zhang, J., Ye, L., & Wu, J. (2008). Toughening epoxies with halloysite nanotubes. Polymer, 49(23), 5119–5127.
CTE and Mechanical in Glassy and Rubbery States Improvement
Halloysite was incorporated in a cyanate ester cured epoxy resin to lower the CTE value and increase the mechanical properties of the epoxy resin.
Sample (wt%) |
E’ at 50C (Mpa) |
Increase (%) |
E’ at 210C (Mpa) |
Increase (%) |
Neat Resin |
2701 |
|
62.8 |
|
4% Halloysite |
3354 |
24.2 |
88.1 |
40.3 |
8% Halloysite |
3491 |
29.2 |
109.7 |
74.7 |
12% Halloysite |
4283 |
58.6 |
139.2 |
121.7 |
Liu, M., Guo, B., Du, M., Cai, X., & Jia, D. (2007). Properties of halloysite nanotube– epoxy resin hybrids and the interfacial reactions in the systems. Nanotechnology, 18(45), 455703.
Impact Strength Improvements
The impact strength of the halloysite particle modified epoxies was noticeably increased 400% without sacrificing other mechanical properties. The underlying toughening mechanisms responsible for the unusual 400% increase in impact strength were investigated and identified as massive micro-‐cracking, nanotube bridging/pull out/breaking and crack deflection.

Ye, Y., Chen, H., Wu, J., & Ye, L. (2007). High impact strength epoxy nanocomposites with natural nanotubes. Polymer, 48(21), 6426–6433.
Flexural Strength and Modulus Improvement
Halloysite was incorporated in a cyanate ester cured epoxy resin to increase the flexural strength and modulus.
Flexural Modulus and Flexural Strength of Epoxy/Halloysite Nanocomposites
Sample (wt%) |
Flexural Strength (Mpa) |
Flexural Modulus (Gpa) |
Neat Resin |
47 |
3.26 |
4% HNTs |
100 |
3.65 |
8% HNTs |
107 |
3.85 |
12% HNTs |
91 |
3.98 |
Liu, M., Guo, B., Du, M., Lei, Y., & Jia, D. (2008). Natural inorganic nanotubes reinforced epoxy resin nanocomposites. Journal of Polymer Research, 15(3), 205–212.