Our new family of high performance THERMOCOMP™ AM compounds addresses the unique requirements of large format additive manufacturing (LFAM). Print parameters and mechanical properties are developed internally using test specimens printed on SABIC’s in-house BAAM® machine, and can significantly aid customers in expediting their material selection and processing optimization. Reinforced with carbon or glass fibers for strength, the compounds can be used for applications in tooling, aerospace, automotive and defense industries.
THERMOCOMP AM compounds based on amorphous resins such as ABS, PPE, PC, and PEI exhibit good creep behavior versus semi-crystalline resins, and reduced deformation under constant pressure. Further, lower shrinkage during cooling means these materials demonstrate greater dimensional stability and less thermal expansion during part use.
- ABS-based compounds provide easy processing, low warpage and good print surface quality, making them good candidate materials for a broad range of applications and tooling.
- PPE-based compounds offer lower thermal expansion, outstanding hydrolytic stability, higher strength-to-weight ratio, and higher temperature performance compared to ABS.
- PC-based compounds deliver higher strength, higher temperature performance and higher throughput compared to ABS and PPE, as well as excellent ductility and a smooth surface finish.
- PEl-based compounds, developed from SABIC’s inherently flame-retardant ULTEM™ resins, provide low thermal expansion, high temperature performance, excellent strength-to-weight ratio, high modulus, and low creep.
Each of the THERMOCOMP AM materials is reinforced with carbon or glass fiber, depending on the degree of stiffness and dimensional stability required. They are potential candidates for elevated-temperature applications such as thermoforming and composite layup tooling.
Mechanical properties and processing information for THERMOCOMP™ AM compounds, including tensile and flexural properties, are developed internally using test specimens printed on our large format equipment (see Fig 1). This insight into process conditions and material performance gives customers confidence in the use of our materials and enables faster machine set up as well as higher print productivity.
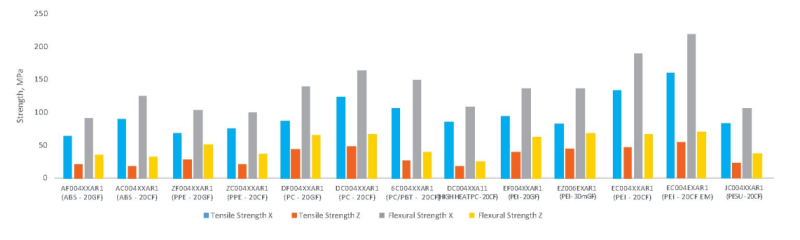
Fig 1: THERMOCOMP™ AM Compounds
SABIC’s access to a wide range of thermoplastics resins and a number of fillers and reinforcements enables development of new compounds to meet customer and application needs for large format additive manufacturing.
Thermoplastic Resins:
- ABS
- PC, PC/ABS, PC/PBT
- PEI
- PSU
- PA11
- PESU/PES
- PPSU
- PEEK
- PPS
- PA6
- PA66
- PPA
- PPE, PPE/Nylon
- Others
Reinforcements - Fillers:
- Carbon Fiber
- Glass Fiber
- Minerals
- Flame Retardants
- Heat Stabilizers
- Uv Agents
- Thermally Conductive Fillers
- Others