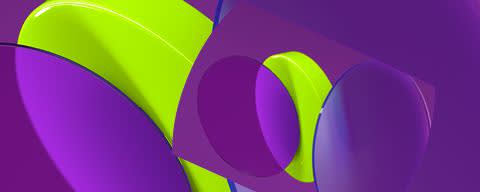
- Polymer Name:Polypropylene Copolymer
- Processing Methods:Injection Molding
- Additives Included:UV Stabilizer, Processing Stabilizer, Heat Stabilizer
- Functions:Resin
- CAS Number:9038-95-3
- Fillers Included:Talc, Chalk, Mineral
- Chemical Family:Polypropylenes (PP), Polyolefins
- Labeling Claims:Azo Colorants-free, Persistent Organic Pollutants (POP)-free, Conflict minerals-free, Azo Dyes-free, PAH-free, PFOS-free, PFOA-free
MOCOM Compounds ALTECH® PP-B A 4430/120 MR30 UV is a Polypropylene Heterophasic Copolymer with 20% chalk, 10% talcum, and UV, heat, and processing stabilizers, as well as easy release (demolding) properties. For injection molding, a melt temperature of 200-250°C and a mold temperature of 20-70°C should be used. This thermoplastic is suitable for building and construction, electrical and electronic, and sport and leisure market segments, and can be used for domestic appliances, gardening tools, and exterior parts. Typical applications include housings, fixing elements, and functional components.