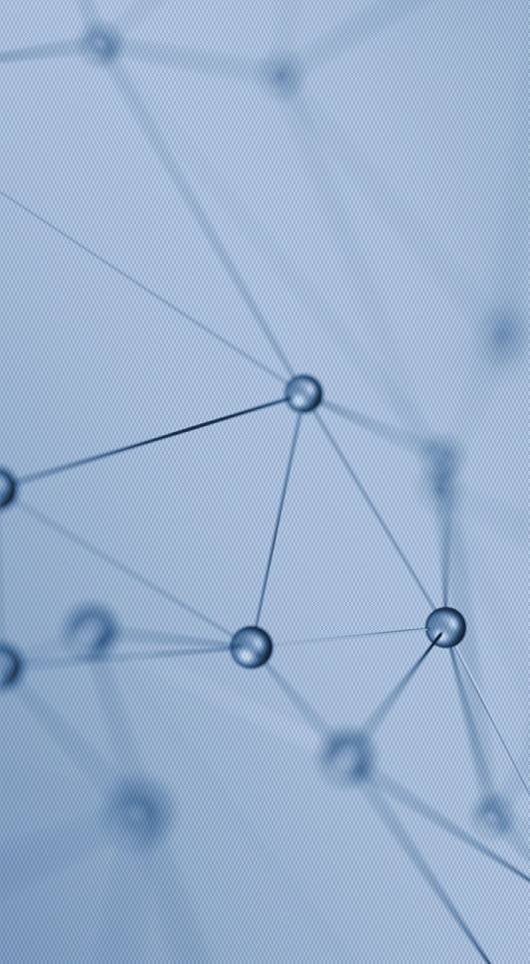
- Chemical Family:Diols, Isophthalics, Glycols, Polyesters, Unsaturated Polyester (UPE)
- Functions:Surface Finish
- Color:White, Blue
- Features:High Strength, Corrosion Resistance, High Durability, Corrosion Resistant
POLYCOR® 960SW Series gel coats are ISO/NPG products formulated for the swimming pool industry. POLYCOR® 960SW Series gel coats meet the EPA National Emission Standards for Hazardous Air Pollutants (NESHAP) for Reinforced Plastic Composites Production - Corrosion Resistant/High Strength or High Performance gel coat. Use of POLYCOR® 960SW gel coat has enabled customers to meet certain requirements of the American National Standard for plastic bathtubs,shower receptors and shower stalls,IAPMO/ANSI Z124.1 .2-2005,Section 6.1. For swimming pool applications,Polynt recommends that these gel coats be backed by IMEDGE® HPB210 High Performance Barrier Coat,Polynt’s ArmorGuard® vinyl ester barrier coat products,or Polynt’s ArmorStar® VSX vinyl ester skin resins. Use of these materials will create a durable osmotic blister resistant composite that is ideal for swimming pool manufacture. These gel coats are intended and recommended only for the original manufacture of swimming pools; they should not be used for post application (other than patching on the original units). These gel coats are not recommended for the manufacture of spas or saunas. While offering these benefits,these POLYCOR® gel coats have retained the important construction and application qualities expected from Polynt Composites gel coats,such as resistance to tearing and color separation,resistance to porosity,sag resistance,consistent liquid properties,and more. These all add up to higher quality appeal in swimming pools made with Polynt POLYCOR® products.