The importance of passenger, occupant and pedestrian safety is driving automakers and their suppliers to upgrade their ADAS offerings to further advance the performance and reliability of assisted driving. As adoption rates rise, the number of safety features and onboard electronic systems per vehicle increases each year, requiring engineers to seek out material solutions for light weighting and increased design flexibility.
Radar systems are an integral part of the ADAS system supporting features such as Adaptive Cruise Control (ACC), Automatic Emergency Braking (AEB) and Forward Collison Warning (FCW). Radar sensors constantly sense the distance between
vehicles in real-time to improve driving efficiency and safety. Therefore, these units require material solutions offering effective Electromagnetic Interference (EMI) shielding and radar absorption properties to ensure that cross-interference does not disrupt the various system components that protect drivers, passengers an,d pedestrians.
SABIC’s highly specialized thermoplastics can help engineers improve radar sensor technologies using materials that aid in light weighting, metal replacement and improved design flexibility. Providing automakers and their suppliers with high performance solutions to help them address the ever-changing ADAS landscape, as well as to identify potential system cost reductions.
Our portfolio offers:
- EMI shielding to eliminate cross talk
- Radar absorption to reduce cavity resonance
- Thermal conductivity for heat management
- Superior mechanical properties and resistance to commonly used automotive chemicals
SABIC Solutions for Radar Sensor System Applications
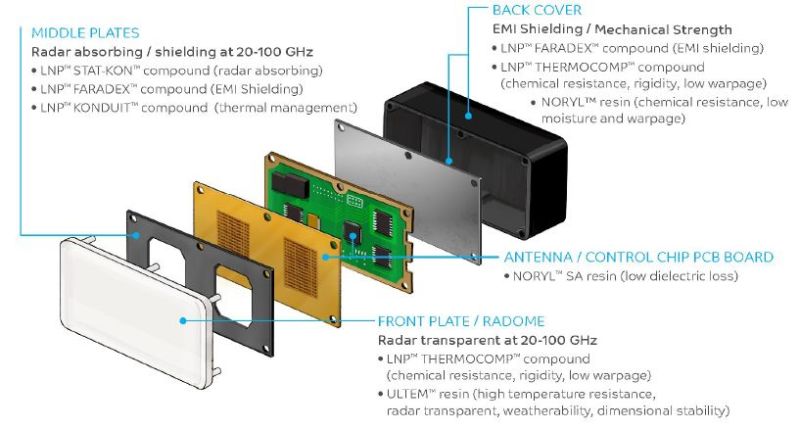