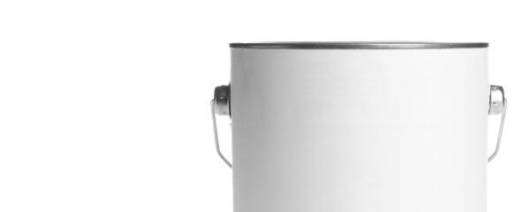
- Brands:1
- Products:5
- HQ:United States
"Flame Safe Chemical manufactures a complete line of fire retardant coatings, fire retardant penetrants and fire retardant sprays that meet or exceed industry’s fireproofing standards. The effectiveness of Flame Safe’s fire retardant products are well documented. The uniqueness of Flame Safe’s products are not only their simplicity of application, their low cost, their environmental safeness, their tested, proven certifications, but most importantly they are required by code. Fire codes are written and enforced to save lives and property
Uniquely, Flame Safe’s fire retardant coatings, sprays and penetrants are easily applied, colorless, non-toxic, environmentally safe, and are aqueous based fire retardants chemicals.
Flame Safe has both interior and exterior fire protection coatings, penetrants, and fire retardant sprays for wood, wood products, lumber, plywood, wood shingles, timbers, fiberglass and plastics, styrofoam, canvas fabric, thatch, thatching, tiki huts, paper, cardboard and packaging systems for combustable liquids. The Fire Buster™ is a fire retardant treated fabric available for commercial and residential use."