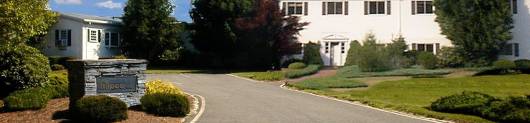
- Polymer Name:Polyurethane (unspecified)
- Processing Methods:Vacuum Casting, Casting
- End Uses:Toys, Prototyping, Agricultural Applications, Housings, General Purpose
The ULTRALLOY series of liquid molding compounds are tough, fast cycling, low cost, and easy to use. ULTRALLOY is designed to be used with Liquid Molding, open casting, pressure casting, or vacuum casting processes. ULTRALLOY can be used with silicone, epoxy, urethane, polyester, or aluminum molds. Low cost molds and fast cycle times are two key attributes of ULTRALLOY.ULTRALLOY is available in several series. Each series has different products with different physical properties. Properties such as elongation, tensile strength, and modulus of elasticity can be selected to mold parts with the correct physical characteristics. Choose the ULTRALLOY material with the exact properties you need, or that are required to meet specifications.ULTRALLOY is available in opaque white, clear/transparent, and in fire retardant (UL 94V-0) versions. Custom coloring can be achieved by pigmenting ULTRALLOY with Hapco's easy to mix color dispersions. Both opaque and translucent color dispersions are available.ULTRALLOY can be molded in inexpensive molds, reducing total part cost, for short run programs.ULTRALLOY is made for prototypes and short runs of plastic parts. ULTRALLOY fills the need for low cost, high performance parts, in volumes less than 10,000 parts per year.ULTRALLOY 100 SERIESA series of general purpose Liquid Molding Compounds. This product turns a natural white but is available pigmented white for extra brightness. Both versions are available in an 8.5 minute or 25 minute gel time.