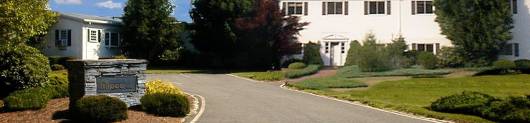
- Polymer Name:Polyurethane Thermoset Elastomer (unspecified)
- Processing Methods:Vacuum Casting, Machining, Thermoforming, Casting
- End Uses:Gaskets, Seals, Molds/Dies/Tools
- Features:Low Temperature Applications, Mercury Free, Low Shrinkage, Low Viscosity, Shock Resistant, Abrasion Resistant, Fast Curing, Good Flexibility, Moisture Resistant, Good Toughness
The Hapflex 500 series offers a full range of soft durometers, from 45 - 95 Shore A, while the Hapflex 600 series yields harder durometers on the Shore D scale ranging from 50 - 70 Shore D. All are relatively fast, room curing, flexible systems that do not require post curing, but can be accelerated with moderate heat for faster curing. Most Hapflex 500 & 600 products are offered in 2 speeds: a standard 30-45 minute working time, and a 3-6 minute working time for fast demold.The Hapflex elastomers are low viscosity, making them easy to handle and pour, yet still provide precise duplications of surface details surface finishes.In addition, the Hapflex elastomers are virtually shock resistant and unbreakable, making them exceptionally well suited for permanent molds, parts or master patterns that will not crack or chip during use or storage. A major advantage is the superior abrasion resistance properties of the Hapflex elastomers.Precision tracing patterns, roll coverings, fixtures, flexible parts, forming dies, bending tools, and a variety of foundry applications are just a few examples of Hapflex applications.