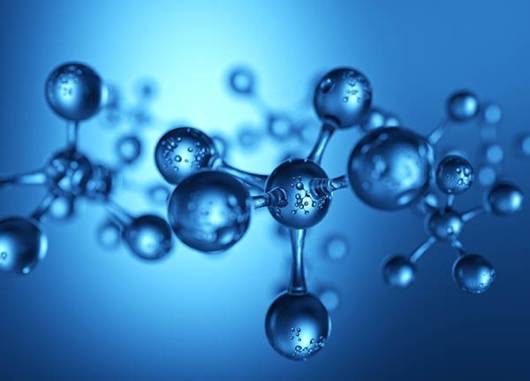
- Polymer Name:Polyphenylsulfone (PPSU)
- Physical Form:Parts & Shapes
- Features:X-Ray Sterilizable, High Ductility, Biocompatible, Gamma Sterilizable, Hydrolysis Resistant, Life Science Grade, Plasma Gas Sterilizable, Acid Resistant, Alkali Resistant, Steam Sterilizable, Ethylene Oxide Sterilizable, Heat Sterilizable, Excellent Sterilization Resistance
- Density:1290.0 - 1290.0 kg/m³
- Tensile Modulus:2450.0 - 2450.0 MPa
- Color:Grey, Blue, Off White, Yellow, Green, Orange, Brown, Red, Black
Sultron® LSG R5500 PPSU Black BK937 is designed for healthcare and pharmaceutical applications. It offers numerous features, including high ductility, ethylene oxide sterilizability, biocompatibility, hydrolysis resistance, excellent sterilization resistance, X-ray sterilizability, alkali resistance, life science grade, gamma sterilizability, steam sterilizability, acid resistance, heat sterilizability, and plasma gas sterilizability. It comes in various colors, including gray, black, orange, brown, blue, red, green, yellow, and off-white, and is a product available in the physical form of parts and shapes.