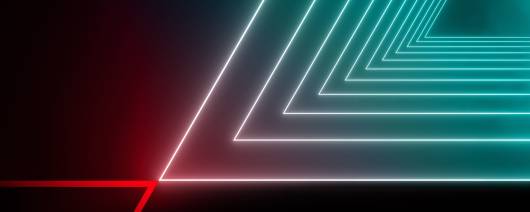
- Polymer Name:Polyphthalamide (PPA)
- Processing Methods:Injection Molding
- Flexural Modulus:40000.0 - 40000.0 MPa
KyronMAX® S-4330 is a high-performance polymer that combines the excellent strength, stiffness, and thermal resistance of high-temperature PPA (polyphenylsulfone) with the added strength and stiffness of ultra high-strength carbon fiber. This injection molding compound is designed to excel in demanding applications where high strength, stiffness, thermal stability, and chemical resistance are required, especially at high temperatures.Key features:Ultra high strength: carbon fiber reinforcement provides added strength and stiffnessHigh-temperature PPA base: provides excellent thermal stability, dimensional stability, and chemical resistance at high temperaturesInjection molding pellets: allows for easy incorporation into your designs and efficient productionHigh temperature resistance: able to maintain stability and strength at high temperatures.Benefits:Improved strength and stiffness of components in demanding environments and high temperaturesIncreased resistance to wear and tear and high temperaturesEnhanced performance and durability of your products in high temperature and chemical environmentsPossibility to design and manufacture complex geometriesApplications:High strength structural components in the automotive, aerospace, and industrial industries, where high temperature and chemical resistance is requiredComponents that require high strength and stiffness, such as gears, bearing components, and bushings in high temperature environmentsIndustrial and manufacturing equipment where high strength and stiffness is needed, such as in high temperature environments and chemical processesElectrical and electronic components where high temperature, chemical and dimensional stability is needed, such as in high temperature motors and generators.KyronMAX® S-4330 is a versatile and reliable material that can help improve the performance and longevity of your products. It's only available in injection molding pellets form, it allows for efficient production and the ability to create complex geometries.Please note that no stock shapes are offered