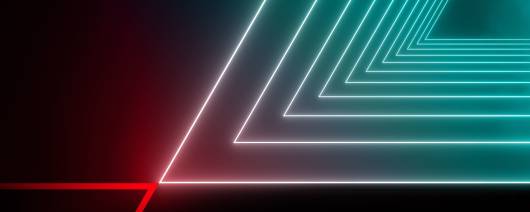
- Polymer Name:Polytetrafluoroethylene (PTFE)
- Physical Form:Rods, Tube, Plates
- Features:High Performance, Good Mechanical Properties, High Stiffness, Low Coefficient of Friction, High Strength, High Tolerance, Anti-Wear Properties
- Density:1890.0 - 1890.0 kg/m³
- Tensile Modulus:1.238 - 1.238 MPa
- Color:Black
Fluorosint® 135 is an advanced polymer material that combines the excellent chemical resistance, low friction and high temperature properties of PTFE (polytetrafluoroethylene) with the added low coefficient of friction, strength, stiffness and high pressure velocity capabilities. This material is designed to excel in demanding applications where high performance and reliability are required.Key features:Low coefficient of friction: provides excellent wear and deformation resistanceHigh strength and stiffness: provides superior mechanical performance at elevated temperaturesPTFE base: provides excellent chemical resistance, low friction and high temperature propertiesStock shapes available: allows for easy incorporation into your designs and efficient productionHigh temperature resistance: able to maintain stability and strength in high temperature environments.Benefits:Low coefficient of friction, making it ideal for seals, bearings, and washer applicationsImproved strength and stiffness of components in demanding environments and high temperaturesIncreased resistance to wear and tear, impact and high temperaturesEnhanced performance and durability of your products in high temperature and chemical environmentsImproved reliability and safety in critical applications.Applications:Low friction seals, bearings and washer applicationsHigh-performance wear applications where extreme conditions are present such as high temperature, pressure and chemical exposureComponents that require high strength and stiffness, such as gears, bearing components, and bushings in high temperature environmentsIndustrial and manufacturing equipment where high strength and stiffness is needed, such as in high temperature environments and chemical processesComponents that need high chemical resistance, low friction, and high temperature properties such as valves, pumps, and heat exchangers.Fluorosint® 135 is a versatile and reliable material that can help improve the performance and longevity of your products. It's available in stock shapes as well as custom shapes, it allows for efficient production and the ability to create complex geometries. It's also important to mention that the temperature and chemical resistance can vary depending on the grade of PTFE used as well as other additives, always consult with the manufacturer for the exact properties of the final material.